Supply Chain Now Episode 366
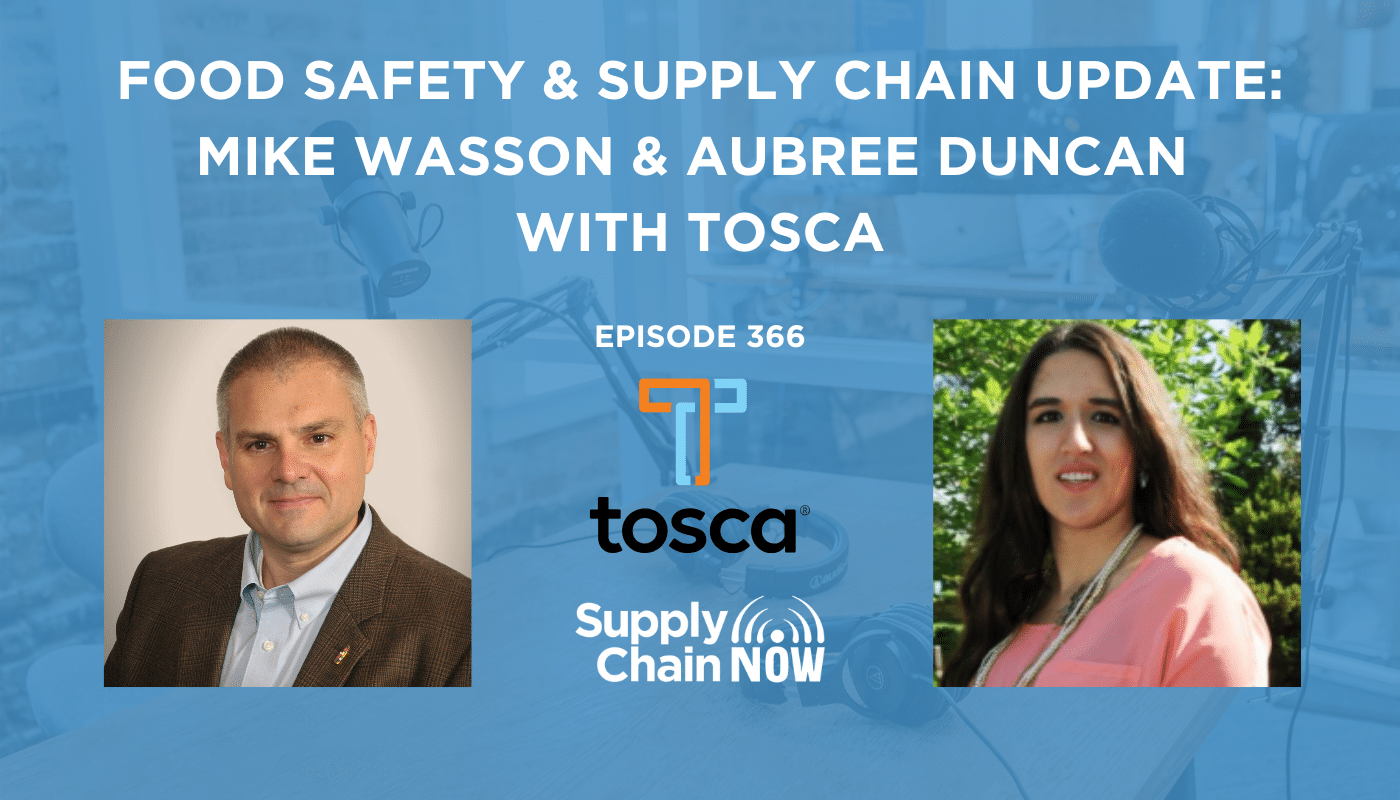
“This [the pandemic] has created a whole new awareness of how dependent some industries are on frontline labor.
– Mike Watson is the Chief Operating Officer at Tosca
Most companies will take any opportunity to remove waste from the supply chain, but there are different kinds of waste they need to consider. Product waste and packaging waste, but also wasted time. All of these are levers available to supply chain teams looking to increase their operational efficiency.
Mike Watson is the Chief Operating Officer at Tosca, a manufacturer of reusable plastic containers (RPCs) used for shipping perishable food, and Aubree Duncan, is a Director of Food Safety with Tosca.
In this conversation, Mike and Aubree share their point of view with Supply Chain Now Co-hosts Greg White and Scott Luton on:
- What their perspective as perishable container producers suggests about fears of a food shortage
- The impact that labor shortages are having on the food wholesale and retail and foodservice industries
- The critical role that infrastructure and logistics plays in ensuring that essential businesses could remain operational through the disruption
Intro – Amanda Luton (00:00:05):
It’s time for supply chain. Now broadcasting live from the supply chain capital of the country, Atlanta, Georgia, heard around the world supply chain now spotlights the best in all things. Supply chain, the people, the technologies, the best practices and the critical issues of the day. And now here are your hosts.
Scott Luton (00:00:29):
Hey, good morning Scott Luton and Greg white with you here on supply chain. Now welcome to today’s show, Greg. Good morning. How are you doing? I am doing great Scott, how are you? Fantastic. Uh, the hits will continue on today’s show. We’re talking about one of the hottest topics, two of the hottest topics. Really both from an industry standpoint and a consumer standpoint, right? The food supply chain and food safety. Yeah. And Greg, we’ve got two industry experts that I think are really going to help us improve our supply chain IQ. Right? No doubt. I can’t wait. I’m afraid. I’m afraid to spoil it. So I’m going to let you proceed cause I want to shout out their names, but let’s roll now. Let’s do it. So real quick, before we do so to our listeners, if you enjoyed this video interview, be sure to check out our podcast. We publish Monday through Friday, sometimes on Saturday, and you can find a sense, subscribe wherever you get your podcasts from. Okay. With no further ado, want to welcome in our guest today, Mike Watson, chief operating officer with Tosca and his colleague Aubree Duncan, a director of food safety with Tosca.
Scott Luton (00:01:38):
Hey Mike and Aubree. Good morning. Good morning. Good to see you. It’s great. Great to have you on the show. Uh, Mike, you, this is, I think your third or fourth appearance. We love our repeat guests, right? I love being a repeat guest as well. Thanks for having me back. And Aubree, your first appearance was supply chain. Now, and I love your background, which we’ll learn more about in a minute. And you know, we’d have not, Greg and I were talking pre-show, uh, Mike and [inaudible], we haven’t had enough experts on the show talking food supply chain and food safety. So I think we’ve got a, we’ve got a great lineup here. Yeah, it’s a, it’s an interesting topic. Uh, on a, on a normal day, I think it’s an interesting topic and right now with everything going on, I think that’s particularly sensitive. Yeah, agreed.
Scott Luton (00:02:27):
Agreed. But it’s on, you know, it’s, it’s, uh, just like the term supply chain is on the tips of more tongues than ever before. I would think that even for even consumers that aren’t involved in supply chain, uh, are thinking a lot more than they typically do about food supply chain, food safety, and what lies ahead. So appreciate y’all coming on and sharing your expertise and some of your insights. So, uh, Greg, before we get started, let’s get to know Mike and Aubree a little bit better. So, Mike, let’s start with you and folks that have seen you, uh, your earlier appearances will know you a little better than some that are new of course, but, you know, give us a refresher. Tell us about Mike Wasson a little bit.
Mike Wasson (00:03:05):
Yeah. So, uh, I’m the COO with Tosca, uh, been, uh, been with Tasco about six years now. And prior to that, um, some just fantastic organizations that I’ve worked with, including the Coca Cola company. Uh, DHL roadway express. Um, uh, great, great trading organizations, great learning opportunities for me. Uh, also currently the, uh, the chairman of the reusable packaging association, which is a tremendous, uh, uh, trade association, uh, furthering the cause of reusable packaging and eliminating one way packaging. And then the chair elect, uh, for the association for supply chain management. Uh, and, uh, been been in the industry much, much longer than I’d care to admit.
Greg White (00:03:49):
We always say more than two decades, Mike and our, our agreement with all of our guests than never say more than that. That’s right. That’s coming up on two decades, give or take,
Scott Luton (00:04:01):
you know, really given all of what Tosca is doing and all the growth there. Uh, and then to, to be involved at it, senior leadership with two rock and roll organizations such as re reusable packaging association and of course, ASC. Um, I really don’t believe you get any sleep at all, Mike, or you’ve got two or three clones. I don’t know. One of the other,
Mike Wasson (00:04:20):
well, I’ve got a very supporting family, a beautiful wife and daughter. Uh, and a, uh, just a phenomenal team. At the, at Tasca that that helps keep things moving along nicely.
Scott Luton (00:04:30):
Outstanding. Hey, real quick. Arbery um, cause both of those organizations are great resources. Of course. [inaudible] dot org is a great resource for our listeners to check out a variety of supply chain thought leadership. What about, uh, how can folks learn more about RPA?
Mike Wasson (00:04:46):
Yeah. Uh, it is, uh, uh, reusables uh, right. So and actually if you just go type in reusable packaging association, that’ll take you right to the left.
Scott Luton (00:04:54):
Perfect. Okay. Aubree, same question to you. So welcome supply chain. Now looking forward to your, uh, your perspective today. Tell us about yourself.
Aubree Duncan (00:05:03):
Thanks. So I’m Aubree Duncan. I am the director of food safety at Tosca. Uh, I’ve been with Tosca for three years. Prior to that I have about, uh, six years of industry experience in the food industry. Um, I’m also on the RPA food and beverage committee as the lead chairperson. And uh, I’m really excited to talk about food safety as one of the biggest concerns people might have when they’re buying through to the grocery store, especially during a pandemic. Um, and from experience I can say that most of us never anticipated that something this large would impact our business and day to day lives.
Scott Luton (00:05:41):
Mm mm. Uh, just a little bit of passion there, Greg. Huh.
Greg White (00:05:44):
Yeah. And expertise too. I mean, it really impressive this relatively early in your career though, I’m sure it doesn’t seem like it to you to have done some of the things that you did. I got to surface this. So tell us why you’re so driven and why it’s this progression has been maybe easier for you than it might for some.
Aubree Duncan (00:06:10):
Uh, I think the biggest reason I’m so driven is I was a student athlete in college. Uh, I was a swimmer at Virginia tech and I’ve been competitive swimming since I was 12 years old. Uh, so it’s kind of natural to me to want to be the best in whatever I do. And I’ve always loved food, so I thought, you know, that’s great job stability. Um, like to do good, make sure people are safe while they’re eating their meals.
Scott Luton (00:06:34):
Love that. When you working out at five o’clock in the morning, she was meant for supply chain since 12 years old. Alright. Alright. So Mike, before we dive into a food supply chain, food safety, some lessons learned and, and the path forward, uh, let’s make sure we understand in a nutshell what Tosca does. So Mike, tell us more about Tasco.
Mike Wasson (00:07:03):
Yeah, so a Tosca, a reusable packaging company, right? Uh, we, we are the, uh, the provider of, uh, RPCs are reusable plastic containers. We’ve been in business, uh, gosh, coming up on 61 years in, in June that we’ve been around. Um, and, and our, our job is to provide innovative packaging solutions, uh, that help optimize, uh, supply chains through, through, um, uh, retailers and suppliers and providers primarily for perishable food. Um, we, we partner with some of the largest retailers, the largest suppliers, uh, the largest processors, uh, largest farmers, uh, all across the world. Uh, and we are a global organization as well. Uh, so we’ve got the kind of presence in Europe, in the middle East and, and, uh, all of North America. Uh, and, and really at the end of the day, our goal is to eliminate waste throughout the entire supply chain, again, primarily in the perishable food space. Gotcha. Okay.
Greg White (00:08:04):
I think the interesting thing about what you do is you can see what you do every day. You go to the grocery store, especially when you pass w what I think of from the last time you were on the show is eggs, right? And the brilliance of the engineering of that, that carton container, whatever you want to call it, that allows you to position the eggs to ship and store and position the eggs in the store without ever taking them out and risking breakage. So in there, there are a lot of benefits aside from the sustainability of reusability in terms of protecting the food as you, you know, as you deliver and store it as well. Right?
Mike Wasson (00:08:45):
Yeah. And, and not, not to be a plug for Costco so much, but, but when we talk about eliminating waste through the supply chain, the big waste component is food. Um, but by, by shipping in our containers, we don’t damage food through transit. Uh, eggs of course being the most, uh, the most breakable, but, but meat for example, when meat, uh, travels, it can get bruised easily. And when it gets bruised, it gets marked down. People don’t buy it. Um, but, but we’re, we’re not just in those visible supply chains like eggs. Uh, we ship produce, uh, we ship meat, we ship popery, we should have seafood, uh, eggs, uh, cheese. Um, I think that’s probably the big things, right? Um,
Greg White (00:09:31):
no bacon. Is there any way we could get you to that?
Mike Wasson (00:09:34):
So bacon, um, but, but then globally too, we’re, we’re in bread, uh, beverages, um, and actually globally and a lot of non-perishables as well. Uh, garments and pharmaceuticals and cosmetics and, and things like that. Just anything where we can take waste out of the supply chain. Uh, and again, waste, not just food waste, but labor waste as well. You know, waste taking miles out of the, out of the transit, uh, adding more cube utilization on a, on a truck. Um, you know, labor in, uh, in, in Greg, the example you gave of the eggs where it’s a retail ready package that they put it in the cooler, drop the wall and it’s ready to go. Meaning you don’t have utility knives in the hands of the store, workers cutting open boxes and stacking, which is not a terribly value added service. And I think we’ll probably get into this a little bit today, right, with labor challenges, uh, and trying to minimize contact. If you can set a product in a cooler and walk away and go to another value added service or there, there’s a tremendous amount of value in that and a tremendous, tremendous amount of waste if you’re, if you’re not doing that. Right.
Greg White (00:10:48):
Well, and, and to your point, we’re going to dive right into that. And Greg’s gonna gonna lead us off here, but before he does, uh, Mike, you didn’t tell me you were bringing one of your supply chain planners who evidently is waiting very patiently to be interviewed right behind you.
Mike Wasson (00:11:01):
Yeah. Yeah. That’s the, uh, the funny story behind him. Uh, so it many, many, many years ago I bought a matching set of the cigar store Indian and the, and the cowboy and I ended up with the cowboy and the Indian is still in, uh, in my mom’s basement up in Ohio.
Greg White (00:11:20):
Wow. Who Mike Watson is by looking at the background. Right. Well if you, if you look off on the other side, you really, there’s quite a, quite an assortment of, uh, of stuff over it. I love it. Well, Greg, take us away. Dive into a Fitch blockchain. Well, so you know, to segue just a little bit, I think it’s interesting that we’re talking about food waste because one of the big topics during this coveage, um, this coven pandemic is the issue of food not getting to the market, not getting to the consumer and going to waste on the ground or you know, at the dairy or, or wherever else. So anything we can do in that regard is valuable. But at the same time, we’re talking a lot about food shortages and we hear this all the time. The supply chain is broken or the supply chain is breaking or whatever it is. So let me just ask you, and I think, I think I’m going to flip the script a little bit, Mike. I’d like to ask Aubree this. Um, are we going to run out of food?
Aubree Duncan (00:12:26):
So the short answer is no. Uh, but the food supply chain is pretty complex. Uh, so a lot of people have seen in the news that milk’s being dumped, fields are being plowed. Um, we’re talking about livestock D population. Um, but there’s some things to consider. So we are processing at slower efficiencies because we’ve put social distance in place. Some of our processors have shut down. Um, and those materials can not be converted raw to raw goods. And because that’s happening, we see a shortage with an uptick in demand. So people are panic buying and we can’t meet those needs. Our grocery supply chain is meant to be just in time, so they can preserve freshness and quality of the product that we’re buying, especially in perishables. And they want to limit waste. So if they stock up on six months worth of salad, it’s probably going to go bad.
Aubree Duncan (00:13:17):
They’re going to lose money and they’re going to have food waste. Um, we also know that our supply chain, uh, some products are stored for months before they actually make it to the grocery store. Uh, so we’re talking about grain. Some types of meat are frozen before they’re sold. Uh, and then peak demand. So back in March when this really started happening, people started working from home. We were a hundred percent year over year, last year, sales and retail grocery. Um, and right about now we’re between 20 and 30%, so it’s slowed down a bit and the store should be able to pick back up to meet the regular demand even with efficiencies slowing and, uh, with plant closures.
Greg White (00:13:57):
Hmm. Aubree, aren’t you glad you’re not responsible for toilet paper and paper towels in a grocery store?
Aubree Duncan (00:14:04):
I am definitely, definitely glad.
Greg White (00:14:07):
Who would’ve ever thought that? And you know, that really started the conversation around the supply chain is breaking or broken and then food concerns as well. And I think we’ve seen so many adaptations of the supply chain, not consumers getting involved and distributors distributing direct to consumers as well. Right. So,
Scott Luton (00:14:29):
Oh, real quick on that Greg. I think what’s fascinating about that is uh, you know, the toilet paper manufacturers, they’ve ramped up production, right? Uh, and in times where, you know, unprecedented demand, right? And then you look at a disinfectant wipes and you see what companies like Clorox are doing. Some of these other folks, they know, they found out that the is not going to be just a a blip. They’re projecting demand, a heightened demand for several years. So what are they doing? They’re investing in new production lines to meet that demand for years to come. Wow. Stepping up production in the meantime. So it’s really, you know, it’s amazing to see how supply chain folks, when they, when they, they wrap their head around the data, whether it’s going to be a small little blip or some kind of extensive extended demand and figure out the game plan that that’s what I love about this industry.
Greg White (00:15:18):
Well, that’s what Aubree was just talking about too, is, I mean, you know, the initially produce demand went down dramatically as people quarantined in place. Cause I think they all plan to eat frozen pizzas or something like that the whole time.
Mike Wasson (00:15:36):
Yeah,
Greg White (00:15:36):
that’s right. And I think ultimately people found, they found their, their cooking persona more and they started buying more of the fresh goods that you all protect. Right? And, and then, as you said, panic buying hits, anytime you hear anything about a shortage, of course, even if you wouldn’t have bought a steak before now or you know, or chicken breasts before, now you’re all over it. So, and, and that’s just one of the challenges that that companies face in the food industry. So, Mike, I want to ask you this, and that is, um, in, in the food industry with this pandemic and seismic societal disruption, how are companies maintaining continuity and operations, uh, during this time?
Mike Wasson (00:16:20):
Yeah, and I think, you know, Greg, you and Scott both touched on, um, the supply chain disruption as a whole, right? And, and, uh, an enormous amount of credit goes to the supply chain teams in, uh, the, the toilet paper industry, the paper towel, industry cleaning, disinfecting products, medical supplies, uh, you know, import goods, uh, oil and gas industry, right? Have all experienced just significant, uh, uh, unprecedented disruption in this time in the food supply chain. I think we’ve been hit kind of on both sides, right? The supply side, significant significant disruption, but also significant shift on the demand side, right? So, um, if you think about the supply side, give or take, half of the food that gets consumed in the United States is consumed in the food service sector. And that would include restaurants, institutions, uh, institutional food service, um, you know, cafeterias, break rooms, things like that, right?
Mike Wasson (00:17:25):
And that that demand has effectively disappeared, uh, totally disappeared. The supply chain for that side of the supply is totally different than it is on the retail side. Uh, packaging is different. Uh, standards are different. Uh, regulations are different than the USDA and the FDA, uh, manages those, uh, those channels differently than do retail. The grading of food is done differently. Um, customer expectations are also different, right? When you, when you see two prepared, uh, at a, at a restaurant or a cafeteria, you don’t get to see how it comes, right? So things like the, the, the ugly, uh, fruits and vegetables, right? Well that thrives in that market because you see it prepared, not unprepared, right? So enormous disruption there. Uh, and, and sort of fixing that side of the supply chain has been an extraordinary amount of work for everybody involved. At the same time on the supply side, you’re also seeing significant labor disruption.
Mike Wasson (00:18:32):
Uh, the, the, the supply side of the food supply chain is a very manual operation and a lot of cases, right? You, you have farmers in the field harvesting produce. Um, and all of the supply side has been hit very hard by labor shortages. Um, at the same time we’ve had labor shortages because of pandemic, because of, uh, infection and plants and things like that. We’ve also implemented, uh, you know, border crossing restrictions. We’ve implemented state at home orders, which means that it’s harder for companies to get labor into the plants to help manage this manual piece of the operation. Um, social distancing also a huge impact on the food side. Um, when you’re in a processing plant, uh, and maintaining that social distancing means infrastructure changes, uh, but it also in many cases means slower productivity, right? Take, take half the people off of a production line.
Mike Wasson (00:19:33):
All of a sudden your, your, uh, throughput goes down pretty significantly. Uh, and, and suppliers and retailers have really been struggling, uh, to, to source from different locations to help manage through that, uh, working through the regulatory agencies to make sure that they are implementing, uh, the, uh, the retail standards or relaxing the standards to make sure that they can get that food service, uh, food into the supply at the same time or on the demand side. Right. We talked about, uh, uh, re restaurant and food service and institutional demand has disappeared at the same time. You had that kind of, that early surge that the hoarding, uh, more of toilet paper and implore rocks and things like that. Um, but, but also of food. Uh, and, and Aubree touched on it a lot of, uh, comfort food, a lot of frozen pizzas, shelf stable, things like that. Um, but we’ve also seen, uh, you know, the price of eggs has gone absolutely through the roof. Um, before the pandemic. Uh, you, you could buy a dozen eggs in some stores for, you know, 59 cents, and I think they hit a high of $4 and something just because of that crazy surgeon demand. Uh, and again, eggs is an interesting one because, uh, retail eggs have a different grading system than, uh, than food services and shell eggs versus liquid eggs and things like that.
Scott Luton (00:21:00):
I was reading about that yesterday. I didn’t realize, I think I got these numbers right, Mike. 20% of all eggs go to be liquified. Uh, and, and that, that side has really backed up and is leading to some of these things that Aubree spoke about. Some of the, you know, um, throwing things out in that, that no one likes you and supply any, any supply chain professional. We hate waste, right. In all forms. And, and I think it’s been challenging for consumers to understand the points you’re making, Mike, of why we’re hamstrung to some extent, no pun intended, to, to, to, to uh, connecting these two very disparate supply chains between the food service institutional side and your consumer, your retail side. So I appreciate where you’re coming from and what you’re sharing.
Mike Wasson (00:21:47):
Yep. You bet. I’ll tell you one of the, I think the more fascinating things from a supply chain perspective is the shift from traditional retail to now, uh, online, uh, ordering and, uh, store pickup and home delivery. Right? W we have effectively transitioned retail grocery stores in the neighborhood to many fulfillment centers, right? Which is not what they were built for. Um, you know, companies like Instacart, uh, Amazon, Walmart, uh, target hit target, uh, all up by according to USA today. I just read an article about that, but their sales are up over two thirds versus prior year, which is extraordinary. Um, and, and, and by the way, the Washington household is driven a fair amount of that as well as helping the economy. Mike, uh, companies like Schwan’s that do kind of the frozen, uh, frozen home delivery stuff. I saw that. I haven’t seen a Schwan’s truck in probably a decade and I’ve seen a couple of them now.
Mike Wasson (00:22:48):
Well, we, we signed up, uh, uh, two, two and a half months ago, give or take and have really enjoyed that. Uh, but, but, but again, what’s really interesting is as you shift that, um, that that consumer demand from, you know, push your shopping cart up and down the Isles to online ordering and now your, your local retail grocery store is a fulfillment center. Uh, it’s created a whole new shift in demand for our product, right. Where, um, we, we have a, uh, a reusable grocery tote that’s built for that online grocery fulfillment. Um, you used to only have demand for that in the EU. Uh, w we brought that over to the States. Uh, I mean almost immediately seemed really nice, nice adoption of that and pretty, pretty good growth in that eCommerce space. So,
Scott Luton (00:23:36):
so that was my next question. I think you’re kind of leading to my next question. I’m really interested in how you all, how Tosca and your company, your products are
Greg White (00:23:46):
adapting in this, in this ever changing environment. So tell us a little bit about that.
Mike Wasson (00:23:52):
Yeah. Well, so first let me say, uh, and I want to make sure, um, w we come back to the fact that we, we cannot adapt. We cannot take care of our customers if we don’t take care of our team. Uh, I am extraordinarily proud of the Tosca team, uh, how we’ve stepped up to meet that, uh, that increased demand and they’re shifting demand, uh, for our customers. We have a culture at Tasca of always putting the customer first and having that mindset kind of going into this pandemic really allowed us to continue to operate seamlessly through the disruption. Um, we have an amazing supply chain optimization team, logistics team, transportation team, uh, transportation partners with our carriers and our three PL, uh, our sales. And support team, uh, all in everyday contact with our customers in everyday contact with our 18 service centers across the United States. Uh, using good established SNOP process stuff, uh, to make sure that we never ever missed an order to our customer. Uh, there has not been a single disruption through the entire supply chain in any of the food service sectors that we support, uh, caused by, uh, a gap, uh, with Tosca and with the reasonable packaging. And again, in meat, eggs, produce, poultry, seafood, cheese, always have had those food safe, clean containers to pack their products in. Um,
Greg White (00:25:22):
that’s really impressive. So I got, I got a wonder with, with the changing dynamic in produce and, um, and meat and various other staples bread and things that you, you support, did you see an initial drop in demand or an initial blip and demand? Was there any, anything that kinda stood out at you as you think about the transition through the pandemic?
Mike Wasson (00:25:48):
Yeah, we, uh, the, the fun part about it is we saw different shifts in different supply chains at different times. So to say we saw a blip or a dip is, is not true. It was just an explosion of just all over the place primarily because we saw shifting demand points, not, not a drop in beat demand for example. Um, but a, but a shift where, uh, and you’ve seen it in the national news everyday where meat processing plants have been particularly challenged. Uh, so rather than sourcing from, uh, you know, Iowa, they would source from Pennsylvania or Texas or Florida or wherever, but a lot of movement of those demand points creating a lot of challenges. Uh, and then, yeah, we, we’ve, we saw it. It’s, it’s the very classic, uh, you know, bullwhip effect. Uh, my, my, my friend Dan Stanton would, would referenced the bullwhip effect.
Mike Wasson (00:26:43):
So a lot of initial surge is everybody panicked to go buy stuff and then realizing that online is available and things will get back to some nude normal for, uh, for the retail space. Uh, and then we saw a dip because everybody had, you know, two years of frozen pizzas in their, in their freezer. Uh, and, and then you, there was nowhere else to put the fresh eggs. So we, we’d see a dip and then it, and then it picks back up again. And, uh, we’re still seeing business strong. Uh, and again, because primarily our space is the retail perishable foods, not so much the food service side. Right. So we’re seeing just continued steady growth, uh, steady demand, uh, through that side.
Scott Luton (00:27:23):
So, uh, I wanna I want to transition here a little bit. I want to move over to Aubree and bring her into the conversation talking food safety. So Aubree, I’m gonna give you just a direct question that the consumers really want to know, right? Easy ones. So is the food supply chain safe, Aubree?
Aubree Duncan (00:27:49):
Yeah, the food supply chain is safe. There’s no evidence that suggests that food, any other type of product, packaging or materials can transmit the virus. Um, I think the FDA and Gina’s have said it best. He said, he said in his quota to say, let me assure you first that the U S food supply chain is safe for both people and animals. Uh, there’s no evidence of animal food or food packaging being associated with the transmission of the Krone virus that causes Cobin 19. Um, so we’ve not seen any type of spread. It’s all been community and people to people transmission.
Scott Luton (00:28:26):
Right. And that’s good to know that it’s also reassuring. Uh, you know, we were talking a little bit in the pre show about some of the, the micro bursts we’ve seen at some of the processing plants, which has been challenging. Mike, you spoke a little bit to that. Uh, we also spoke a little bit about how that’s, uh, a curve ball that’s being thrown in, in these unique times to the managers and supervisors at these sites that weren’t built for physical distancing. So it’s, um, it’s important that, that we all know kind of what we’re up against and how it’s not, nothing is just easy. And even though some companies make it seem real easy for same day delivery these days supply, nothing too much. Easy about splotching. Alright. So, uh, tell me, Mike, tell us more about what you’re seeing other companies doing, including what some of the things that task is doing to reduce the impact. And you were talking earlier about the incredible job that Tosca team has done and how it’s so important to take, take, take care of the team. What are you seeing companies do to make sure they mitigate the risk to employees?
Mike Wasson (00:29:28):
Yeah, I think, um, and I’m going to ask Aubree to weigh in on this as well too, because I think there’s maybe two different sides of it. Um, as a, uh, uh, w we are considered an essential service, right? Food services and the packaging side of it. And we have been, I think really fortunate to have had such a great infrastructure in place, but before the pandemic, right? Which allowed us to continue to operate well, uh, for Tosca. And I think you’ve seen similar reactions from a lot of different companies, but for Costco, uh, our, our S and our global operations continue to operate effectively keeping all of our team members and all of our products safe, uh, because of that rigorous food safety management system that we had in place. Uh, and I think an extremely early adoption of, uh, the CDC guidelines really staying in front of that.
Mike Wasson (00:30:26):
Um, w we started, uh, back in March, actually, right after, uh, MODEC, uh, we decided to, to try the work from home for all of our support staff, all of our administrative and corporate folks. Uh, w we decided to try it and, and kind of test the system on a Friday. Uh, and we never went back, right. We, we, we made the early decision that we were going to do everything that we could. Um, and, and since then we have had, uh, daily meetings of our leadership team and our task force. Uh, we were closely monitoring, uh, that the, the world health organization, the CDC, the FDA, uh, other industry trade groups, um, you know, looking for those daily updates, which, uh, and sometimes it’s multiple times per day. Uh, w we have had tremendous communication internally in our, uh, in our plant facilities, right, where where you, you can’t work from home, uh, and provide clean, uh, sanitary safe, uh, food containers, uh, that, that just doesn’t work.
Mike Wasson (00:31:28):
So we’ve had tremendous communication, uh, daily updates, daily department meetings, um, worldwide town hall meetings to make sure that everybody stays, lots of communication. Um, like most other, uh, organizations I think that are seeing an increase in demand. Uh, we’ve implemented, you know, uh, w we call healthy habits, uh, you know, incentive programs and things like that. Not, not to, um, I, some organizations have called it, you know, hazard pay and, and things like that, that that is not all or we don’t believe that there is any additional risk or hazard for coming to work because we provide a clean, safe environment for our employees to come to work. In w w we created a healthy habits program to try and incent our teams not only to be safe when they’re at work, but also turned courage, those safe behaviors when they leave work. And again, because we have a food safe environment, I think adopting a lot of those practices has been easier for us. Uh, but, but, but similarly, we do, you know, every, uh, every shift, every break, every lunchtime, every everything. We’re, we’re down time clocks and badge readers and, uh, foaming and sanitizing all of our equipment and things like that. And, and maybe that’s a good time to hand it off to Aubree and let her detail home or are you working in the office or both or?
Aubree Duncan (00:32:55):
I am from home, so I am working from home. Uh, before this I was traveling between our facilities, probably about 85% of my time. Uh, so this has been a little shift for me, but, um, most of my work can be done from home, making sure we support the facilities. So all of our service centers in the U S are certified to the ISO and safety standards. Uh, and Mike inferred that when he was saying how easy it was for us to switch over and deal with new information for the pandemic. Um, we’re required to have an emergency response program. Typically you see that program dealing with smaller scale emergencies, maybe like forest fires or hurricanes, tornadoes. Um, and certainly we can take those principles and apply them to what’s going on here. Um, so under that plan we’ve activated a risk assessment, uh, not only to our business, uh, but to the product itself to make sure being tainted safety.
Aubree Duncan (00:33:51):
Uh, we’ve looked at developing a business continuity plan that tells us where our highest risk is and what we need to do to make sure we maintain operations. Uh, we put together the dynamic response team, they meet, uh, every day and they get updates from all of our functional departments across the network. Uh, and then we’ve updated a lot of our programs to make sure we meet the FDA and CDC recommended guidelines. Um, so we’ve got a biosecurity program, GMPs and sanitation programs in place. And we’ve done things like require social distancing. Uh, all the breaks, clock ins, trainings are on the floor with six feet apart, no longer in the conference room. Uh, more frequent cleaning. So we are cleaning the lunchrooms and employee entrances after every shift change and uh, open options for face coverings. So some look goal areas have required them. It’s optional for all of our service centers to use those. And the biggest part, and one of the key things is because we are a food safe and we have a GMP program, we normally required team members who are ill to stay home so they’re not supposed to come to work anyways. And we’ve reinforced that with Cobra 19. If they’re showing symptoms, we are asking that all team members stay home, especially if they know they’ve had primary or secondary contact.
Scott Luton (00:35:13):
Yeah. Well, you know, uh, going back to what you shared earlier, and I think it’s important to note, first off that Tasco is a well-recognized leader, a variety of third parties. Uh, from there, the growth to their approach to work for us to be an employer of choice. So in many ways Tosca is set in the bar, which is great to hear and hopefully you’re throwing the gauntlet down. Some companies may be listening to this that are looking for ideas to, to ramp up their efforts, take care of the workforce. So I appreciate y’all sharing, but going back to what you touched on, or you mentioned hurricanes and tornadoes, and we’re in that season. Um, you know, we, we partner with our great friends over at resilience three 60 on, uh, their hurricane or 2020 hurricane kind of things, expect a tropical report. And unfortunately, um, hurricane season’s not being postponed because of pandemic.
Scott Luton (00:36:01):
I’m not sure if you’re all over Bangladesh. Oh, a massive storm was making landfall, I believe yesterday. Uh, and it’s, it is going to make it so much more challenging despite all the challenges we faced to enter in, into hurricane and tropical season. And all of these challenges get compounded by the normal stuff that happens each year. So, um, we’ll keep our finger on the pulse there, but, um, all right. So as we wrap up this, this portion about food safety, and before we move into kind of some lessons learned and what to expect as y’all break out your crystal balls, uh, Mike starting with you, what else are we leaving out? What else is important when we talk about food supply chain during these pandemic times? What have we not touched on, Mike?
Mike Wasson (00:36:46):
Uh, well, so I guess first let me say, right, so I, I do feel like, um, uh, and I appreciate your, your, your acknowledgement Tasco tries to be on the forefront, uh, but we’re also a learning organization, right? So we are reaching out to other industry partners, um, you know, create groups, things like that. We are constantly trying to learn from others as well. Uh, it is, uh, we, we shared a lot of what I think are sort of funny, uh, pictures when you look at him because it, it, it, it looks very different than normal. Uh, some of the things that Audrey was talking about, you know, the, on day one, we started putting, uh, you know, tape X’s on, uh, on break room chairs and tables and, and lines on the floor to show what that six foot distancing looks like before all the sign manufacturers got in the game.
Mike Wasson (00:37:35):
Uh, and, and we, you know, we had handwritten signs and, and again, just just putting marks on the floor to maintain that social distancing. Uh, and then we started actually taking tables out of the break rooms and putting them outside so we could still have, uh, people have breaks and eat their lunch and things like that, but, but keep the social distance. So, so a lot going on there. Um, and, uh, not, not in any way claiming to be the expert on this, but, but we’ve got really good people and really good. W w we have a pretty strong bias for action. Uh, I think, um, and hopefully we see that, not, not, uh, just from me, but from every, uh, every level in the organization has that last fraction.
Scott Luton (00:38:15):
Well my, if I can tell, you know, just this week, the experts are sending different messages. It’s, it’s tough to find true experts in these truly unique times. So I love a bias for action because, you know, every step we take is it going to be, isn’t going to work out perfectly, but if we don’t take them, we don’t learn and we can’t respond and adjust. Um, so, you know, so a company that has a strong bias for action, their workforce is going to be better off. Uh, they’re going to become an expert before other, you know, lagging organizations. So I can appreciate what you’re sharing there.
Mike Wasson (00:38:51):
Yeah. Thank you. But, uh, so yeah, I think your question was what, what else is, uh, what’s important to know? Um, so, so for us, we, we touched on this at the beginning, right? So, so Tosca is all about eliminating waste from the supply chain, um, in the U S and really everywhere in the world, but, but specifically in the U S where our, our strongest market presence is, uh, there is a very large population of food insecure people before the pandemic. Um, but before, before this hit, like one in seven people in the U S, uh, one in seven Americans are food insecure and they don’t know where their next meal might come from. Uh, and that includes like 11 million children, um, elderly, uh, low income families really impacted by food insecurity. And that’s getting worse and worse now, um, now more than ever before, it’s important to make sure that the supply chain works to deliver food from the farm to the fork, uh, mitigating that food insecurity anywhere that we can.
Mike Wasson (00:39:53):
Um, and I think that is one of the areas we, we touched on at the beginning that Tosca is so proud of being able to provide that packaging that, that, uh, it doesn’t eliminate food waste, but it certainly does mitigate food waste through the supply chain. We, we can’t help get it out of the field, uh, necessarily. We can’t eliminate the labor challenges, uh, in some of those areas, but we absolutely can, uh, make it more efficient, more ergonomics, uh, better [inaudible] on, uh, trucks, uh, but more efficiency, uh, from getting it off of a truck and onto the store. Uh, shelf, uh, or, or cooler, uh, to get it to the consumer. Uh, for the eCommerce stuff we talked about getting it, uh, to, to the car, uh, at the store pickup space. Uh, really, uh, I think RPCs make sure that more food ends up going to the homes that need it, and we’re really proud of that. Um, uh, Aubree, I am certainly thoughts here as well.
Aubree Duncan (00:40:51):
Yeah, I think also, so we do know there’s a lot of food insecurity and, um, we don’t like to talk about it. Uh, but we do know that the USDA is trying to help. Uh, thankfully all of that food we talked about that might be getting plowed under because it’s supposed to go to food service. Um, a lot of the acts that have passed to help with [inaudible], uh, a lot of that money is earmarked with the USDA and FDA to go towards purchasing those goods. Um, and they’re taking those goods and they’re putting them into programs that are going to help, uh, help those groups. So they’re going, uh, they’re looking at alternate options, like delivering meals via the regularly scheduled bus routes. Um, they’re letting parents come into schools and pick up a week’s worth of their kids’ meals so that they can have meals at home. Um, we’ve looked at in train, they’ve looked at entering private partnerships with companies to deliver meal boxes, kind of like home chef, uh, because they are on food assistance, uh, snaps, meet online so families don’t have to go into offices to access their food benefits. They can go online, phones or computers. Um, and then all that excess inventory, they’ve earmarked millions of dollars to purchase excess produce protein and dairy.
Greg White (00:42:00):
Right. Love that. That’s, that’s an incredible initiative by the industry. We’ve seen companies built to take advantage of food waste and to deliver valuable and still edible food to people in need. There’s a company here in Atlanta called gooder, Jasmine crow’s the CEO, and that’s what they do. They coordinate with groceries and restaurants and other institutions to take that food and make sure that it gets used. As she said, she quoted hunger is, is not a supply problem. I’m paraphrasing, but problem, it’s a logistics problem. The food is available. 40% of all food is wasted. Right? So we know that the food is available to the 17% of the population, Mike, that you’re talking about. So we know we can get it there. And then we talked also with Terrance whose last name escapes me from love beyond walls and they have initiatives to actually hit the street and, and uh, get people fed and fresh water and that sort of thing. So as we transition here, I want to get a few hot takes from you to so down, you know, high level answers. Aubree, I’m gonna start with you cause you love throwing these tough questions at you. Um, so what is, what is the greatest challenge the supply chain is faced during coven 19, in your opinion?
Aubree Duncan (00:43:28):
Uh, so I think that’s the constant change of the news. Um, and food safety. We already expect that we’re going to have to anticipate change and get ready to change with customer demands or industry regulation. Uh, but with this pandemic, the news is constantly changing, whether that’s on the hour or to the day to the week, uh, regulations from the CDC who, and the FDA have changed from what we saw in March to what they are today. Um, and so keeping on top of that, making sure we’re using reputable sources to make our decisions, uh, and making sure we try to get through all of the weeds and communicate one message to our teams and our customers about what we’re doing.
Greg White (00:44:10):
I think you have to really distill the information you’re getting, even if it’s from expertise and, and authorities and determine what it means to you and your, yeah. So Mike, what’s yours? What do you think is the biggest challenge we face?
Mike Wasson (00:44:25):
Yeah, well I think Aubree hit on the big one, right? And if you don’t like the news, you change the channel and you’ll get a totally perspective on it. But you know, from a, from a supply chain perspective, right. We touched on, um, the, just the constant volatility in the supply chain, right? Shifting, uh, shifting supply, shifting demand. I think those are very short term challenges that the supply chain will face. Right? I think some of that will, we’ll get back to whatever the new normal might look like. Um, but, but that, that’s a question of, uh, you know, working with, uh, truckers and, uh, and drivers and logistics companies to make sure that we’re managing that. Uh, I think the greatest challenge is going to be the labor side of it. Um, right. The, the infrastructure to support the food industry is not built for social distancing.
Mike Wasson (00:45:15):
Uh, it’s really not built for, uh, all of that shifting demand either. Right? If you think about the meat industry, uh, you kind of got a process that, uh, in, in certain areas, right? You can’t pick up a, a herd of, you know, 50,000 head of cattle and move it across country to where the labor is available. Right? It just doesn’t work out really well. Uh, so I think the labor is going to be really tough. I think the travel restrictions where, uh, particularly as we’re bringing in, uh, workers from out of the U S uh, and, and mandating corn teams or 14 day, you know, self, corn team, things like that is going to make it particularly difficult, um, especially from, uh, South of the U S border. Uh, I think there’s going to be a lot of challenges, again, in that infrastructure to create a safe place where workers are ready, willing and able to come back into the space.
Mike Wasson (00:46:10):
Uh, and that’s kind of universal, right? Not just in the processing plants and in the harvest areas and the, um, you know, the, the packaging, uh, space. Uh, but, but even in the office space, and I, I will tell you, um, the, the, uh, uh, the technology to support, uh, working from home, the technology to support, uh, these, these kinds of events, uh, virtually is, has been terrific. And, and what a godsend. Um, our, our sales team, uh, our engineering team that really needs to be hands on is really struggling I think with, with travel restrictions and things like that and are dying to get back to work. Uh, but, but, but I think that’s going to be the biggest challenge going forward is redefining that new normal and creating, uh, a workspace where people are comfortable going back to work and not just comfortable but a safe environment for them to return to.
Greg White (00:47:03):
Yeah, I agree. All right, so Aubree, I’m going to hit you with a tough one again. Yeah. But this, this should come right from your experience or harder wherever you store this information. What, what is the biggest learning that you’ve had during this, uh, pandemic? Yeah, so I think one of the biggest learnings is that, um, I’m really glad that you have a food safety program in place recently. Uh, the
Aubree Duncan (00:47:30):
standard we are certified to with ISO did get updated. Um, we saw a change in that standard to align with their other standards to go from not just looking at the food safety risks, but business risk as a whole. Uh, that really aligned well to what’s going on right now. Um, we’ve also seen that we have programs in place that can be updated. Uh, we do have an emergency response plan and a biosecurity plan. Um, but our bio security is more worried about the product. We’re worried about avian influenza and tomato, Brown rugose fruit briars. We’re not worried about, uh, biosecurity coming from people. Uh, so we’ve seen some learnings that we can update those programs, make them a little bit more effective in the long term. Uh, if something like this were to ever happen again.
Greg White (00:48:15):
Hmm. Interesting. What about you Mike? What’s the biggest learning? I mean, you sit in the executive suite, so you’ve already expressed your learnings about work, work in the future, what you think it will look like. And you must be considering a lot of different things as you try to position the organization to proceed. So tell, tell me what you think is the biggest, most important thing.
Mike Wasson (00:48:37):
Yeah, I mean, I think a couple of different things, right? Uh, one big learning, uh, we we talked about earlier, uh, you know, plowing under crops and deep populating hurts and things like that. Um, we, we have to create supply chain infrastructure that can react to those changes. Uh, McKinsey, um, I think I’m getting this right. McKinsey predicted like a 15% increase in online grocery sales, right? But that again, shifts the infrastructure, creating meaningful Fillmont centers at, at your local retail space, which is different. Uh, and, and we need to make sure that the supply chain is prepared to support that. Uh, and in some cases it is. In some cases, it is not at all. Uh, certainly the, the shift in, um, retail demand versus the, the, uh, food service in the restaurant space is going to create a change and it will never look the same again.
Mike Wasson (00:49:33):
Right? Um, many, many, many restaurants, uh, have, have closed or are going to be permanently out of business, uh, because it’s, uh, it’s a pretty tough market to be in on a, on a good day. Um, and they will never recover. W, which will create, uh, you know, kind of a ripple effect, not just in the food space but in the real estate space and, uh, and all the industries that support the food space. Uh, and it’ll create a shift in labor availability because, uh, that, um, you know, frontline food service worker, not just the servers, uh, the, the, the cooks, the dishwashers, right? All of those jobs will be impacted and that will create a pretty significant shift in available labor, uh, for those unskilled workers. But at the same time, uh, those are the jobs that are going to be, I think, most at risk, uh, as companies look to implement automation, right?
Mike Wasson (00:50:29):
This has created a whole new awareness of how dependent some industries are on frontline labor. Uh, and I think through this, people are going to be looking at how do we make sure that we’re not as dependent on people? How do we put in, uh, automated material handling? How do we put in robotics, uh, things like that so that we’re not as dependent. We pay particular attention to that because, uh, again, uh, reusable packaging and our RPCs are, are much more, uh, standardized and much more easily automated with which is an exciting space for us to be in. Um, you know, I think, um, better business continuity planning, uh, outreach, we kind of touched on that, right? That constant updating, that constant learning as an organization. Uh, my old boss used to say, uh, and, and still a great friend of mine. Uh, if, uh, if the competition learns faster than you do, then you’re at a competitive disadvantage. And I think in this case that’s true, but, but take it a step further, if the consumer adapts faster than the, than the companies do that, then you will be, uh, less valued, uh, maybe diminished in the industry. If the consumer shifts demand and the consumer learns more about food safety and learns more about online shopping and things like that, and they do that at a faster pace than an organization does that you’re, you’re going to find yourself out of business I think, fairly quickly.
Scott Luton (00:52:00):
All right. So I want to piggyback on that because, uh, earlier this week in the supply chain buzz, we featured a quote from Jeff Bezos, uh, and whether you like what Amazon is doing in some ways, some ways, or you don’t like it, he’s got a great quote and you can see it in their culture and, and it’s gotten a lot of feedback in our, in our listenership. So, uh, Jeff said a quote being wrong, and this kind of falls in line with what you’re saying. In some ways, Mike, quote, being wrong might hurt you a bit, but being slow will kill you. If you can increase the number of experiments you try from a hundred to a thousand, you dramatically increase the number of innovations you can produce. And, you know, I think w w as we shift gears, as we start to wrap up the interview and we look forward to silver linings and all of this, you know, um, perhaps, and, and not that we would ever want to pandemic to do it, but perhaps the industry needed a kick in the seat of the pants to stimulate some innovation.
Scott Luton (00:52:54):
Right? Uh, Mike, I love how you talked about how you’re going to see these two disparate, uh, supply chains that serve the food industry. How we’re going to figure out how to bridge that so you can, we can pivot much more effectively. I love that. I think it’s going to require like any big supply chain changes often do while the consumer is the North star. And it’s all about the voices of customer. Still with some of these, with some of the ways that we’re going to have to meet the demands, whether we’re talking about reassuring the near shoring, the consumers are going to have to accept some of the things that come with that, including our prices with some things. So it’s going to be a fascinating, um, we’re all, we all can’t wait to get into the new normal where things are going to be different and get past this, this current state where we’re, you know, a lot of folks have been, have been suffering, but there’s going to be a lot of really interesting lessons learned, case studies, innovations that come out of this. But so along all those lines, sorry, uh, let me get on soapbox there. But, but Aubree wanna start with you. When we think about silver linings from the pandemic environment gimme gimme gimme your, your favorite several line maybe in all this.
Aubree Duncan (00:54:03):
I think the technology aspect, um, Mike’s mentioned this a couple of times, but the ability to leverage technology like this or Microsoft teams has really been key to success at Tosca. Uh, we’ve been able to communicate information quickly and accurately. We’ve been able to collaborate across different functions. Uh, and I think that’s really been important in this role because it’s minimize the disruption to our day to day business.
Scott Luton (00:54:28):
Hmm. I love that. And I think, um, there is, it’s amazing to see Greg, we talk about as quite a bit, uh, how folks use zoom has made a fortune. Everyone’s jumped on there, but there’s been a lot of different ways that folks are leveraging technology in this, uh, in this environment that you want to comment real quick for a move over the mic.
Greg White (00:54:47):
Even even the opportunity to recognize that you need technology. I mean, let’s, let’s look at what is the core problem. This is a quick hot take in grocery retail is that replenishment is largely manual and that they don’t know some foundational things like how many cartons of eggs they have in a system right now. And that is a particular exposure in North America, particularly the United States because in virtually every market in the rest of the world, they know those things. And hopefully this, the silver lining is that the grocery industry will shift from their ancient, literally almost 200 year old system of having someone else manage your inventory for you to using technology to do that, which creates the kind of adaptability and the information upstream in the supply chain that allows you to respond much more quickly.
Aubree Duncan (00:55:46):
I, I D I definitely think they will. Um, so the FDA has earmarked a, what they’re calling smarter food safety as one of their key initiatives, uh, from the updates. Uh, so with FDA adopting it, we, and the rest of us in the food supply chain are going to have to adopt that. Um, so they are, you’re marking that it’s on their agenda. They know there needs to be some updates and I think the coven 19 situation will definitely make that go faster.
Scott Luton (00:56:12):
Love that. Love that. Um, okay. So Mike, we’re, as we’re wrapping up on some good news here, we’re talking about the silver lining from the pandemic environment, especially in supply chain. What’s, what’s one of your favorite stores here?
Mike Wasson (00:56:28):
Uh, boy. Well, yeah, you know, it, it’s, uh, I think while we’re still in the middle of it, it’s hard to talk about silver linings, right. But, but certainly can talk about maybe some of the high points. I think, um, Aubree touched on a few of them, uh, that, that the technology that the connectivity with our teams has been, has been terrific for, for me, the, the silver lining is that, um, th th this pandemic will create a new, uh, work life balance right. For, for most all workers, right. Um, the opportunity for me, uh, to, to be at home, working from home, having dinner with my family every night. Uh, it’s created a new normal for me. Uh, I, I think it’ll create a new normal, uh, and we will come out of this I believe, stronger than we were going into it. Uh, w we continue to learn and grow not just as a, as a company or an industry, but as a, as a people, as a country.
Mike Wasson (00:57:22):
We continue to learn from different countries. I think, um, th this pandemic in in some unique way will create a more, um, more of a connected world, right. Not to get, maybe, maybe too philosophical here, but, uh, but we’re learning from other countries. Uh, we have, uh, not just the local calls here, but we talk to our plants and our teams, uh, all over the world learning from what’s going on and, and how, uh, Italy and Germany and the UK and Israel and others are all learning from this and how they’re adapting and how they’re implementing, uh, social distancing and implementing return to work policies and things like that. So I think that might be a silver lining as well, is that maybe we won’t be quite as, uh, proprietary. Nick, maybe we’ll share a bit more than we have in the past.
Scott Luton (00:58:15):
That interesting observation and it definitely will. We’ll be keeping our finger on the pulse for that. I liked that the first point you were making about the work life balance. We spoke yesterday or this week with our buddy ward Richmond, who spent 70 days on the road, um, uh, and, and how he’s enjoyed home officing and seeing his family much more often and much more consistently and how it’s changed, um, the dynamic there in a, in a very good way. And, and, um, you know, there’s good news out there. You gotta seek it during these challenging times, but there’s certainly plenty of good news and the industry will be, you know, um, you hate to go through a pandemic for, to have an industry improve itself. Like it will, but, you know, the industry is going to be a lot stronger coming out of this eventually than it was, uh, you know, just 12 months, six months ago. Um, alright, so, uh, Greg, what a, uh, what a conversation. One that we haven’t really had enough of own the food supply chain here on the show really have enjoyed Mike and Aubree’s take. Huh? I think that’s the interesting thing about it is
Greg White (00:59:22):
we haven’t really talked about food safety and the detailed logistics of retail and I think it’s important for consumers to recognize that as well. So yeah, that’s been really valuable info.
Scott Luton (00:59:35):
Yes, thank you both. And thank you for what you do. I think that point you just made there, I think consumer education in terms of how supply chains work and what’s behind it, I think that’s going to be another silver lining. All this. And it’d be, that’d be good for industry, right? We’ve seen a resurgence of interest. We know we’re gonna need a lot more top talent coming into the industry and that’s, you know, yet one more silver lining here. Okay. So as we wrap up the segment, we want to make sure our listeners know how to get in touch with you both and learn more about Tasca and Aubree, let’s start with you.
Greg White (01:00:05):
Yep. So you can reach out to me on LinkedIn and we also have more information at our Tasco website
Scott Luton (01:00:11):
outstanding. That is Tosca ltd.com, right? Yes. Outstanding. And Mike.
Mike Wasson (01:00:18):
Yeah. So, so also LinkedIn and I do just really quickly, I want to touch on Greg’s point, right? I think we will learn, uh, but, but we cannot take care of the consumer. We cannot take care of business. We can not take care of the food safety and the food supply chain without taking care of our people first. Right. And hopefully that’ll be another big lesson learned for organizations large and small, is to take care of it and invest in your people. Uh, and they will take care of you and they will take care of your customers for you as well. Right? Uh, but anyway, LinkedIn would be the place to find me. Uh, Tasca ltd.com or M [email protected].
Scott Luton (01:00:57):
Outstanding. Well, really appreciate that perspective. I love wrapping up on that note because it is all about protecting the workforce and beyond protecting them, appreciating what they do, you know, from the truck drivers to the pickers Packers to the forklift drivers, to the folks in production and processing, you name it. It’s all about the global supply chain community. That’s right. And then folks at the head of the registers, I mean man on the moon. Right, right. That’s right. Yeah. I’m the same. Amen. Yeah. Um, okay. So with all that said, one of the thank our guests here today, Mike Walston, chief operating officer with Tosca and his colleague Aubree Duncan, director of food safety with Tosca. We look forward to having you all back on. Maybe especially as we get into late 2020 we’ll have you back on to kind of give us your latest insights in, but thank you so much. Thank you for having me. Appreciate it. Alright. Take care. Wow. What a conversation that is tough to get all of that information about an industry that is, everyone’s trying to get as much information as they can because we all experienced stores and grocery stores and food, right. Supply chain. A lot of good stuff there.
Greg White (01:02:13):
Well, when people think about retail, they think about supply chain. So are, or they think about grocery. So yes,
Greg White (01:02:19):
you have to acknowledge that that is one of our top and favorite. Um, and most relevant discussions around supply chain and retail is yeah. Is grocery. Uh, you know, I think consumers have to recognize too that the, some of what we talked about there [inaudible] as you said, Scott, it’s dependent on their tolerance for Mmm. Paying a higher price because the two industries that Mike talked about frequently, frequently food service and food, a distribution, the distributors in those industries literally make no net margin. They have to forward by inventory. Yup. In many cases, to have any kind of margin to pay everyone. So, so it’s gonna it’s going to be painful. If we want those solutions, we’re going to have to be really creative. There’s no silver bullet. It’s not that we’re going to cross every single item in food service, right, with grocery distribution. We’ll find the right places to do that and create those efficiencies.
Greg White (01:03:20):
Yeah, great point. You know, I tried to weigh in earlier because I think a lot of our listeners may not know just the, the global grocery and retail experience. So you have a, and w I won’t say a, what’s our go to no more than two decades or what have you. But you know, you’ve worked with retailers here in the States and Europe and really globally. So I enjoy kind of how you and Mike and Aubrey kind of tackle this, this conversation here today. Okay. So really briefly as we wrap up here today, you know on stuff. Yes, that’s right. And you know, our supply chain trivia is our 1% is so much different than all the rest of our content. We’re trying to meet the demand. We see where folks want to distress a bit. They want to, they want to enjoy some comradery and some fellowship with the, with their fellow supply chain professionals, which by the way, you don’t have to be a supply chain professional, Scott.
Greg White (01:04:14):
Um, I’m just looking to watch anything that even remotely approximates sport and this has every bit of that smack studying, you know, working out people challenging one another and a really amazingly competitive spirit among really knowledgeable supply chain pros. So it’s a blast to watch. You are correct. So big, high five to our reigning champion. Coby cannoli. Got every question right in the last contest. Um, our next challenge is our Eastern hemisphere edition June 3rd 9:30 AM Eastern daylight time. We’re partnering with st pics, which is doing some awesome things in them that could have woods, uh, especially Africa, uh, when it comes to supply chain, moving the industry forward. Uh, so 9:30 AM Wednesday, June 3rd and, but before we get there, uh, tell us about this, this webinar coming up May 27th grade. Well, you know, Gartner has recently released their supply chain top 25 for 2020. We are going to meet with the the curator and master of ceremonies, Mike Griswold who runs and presents this amazing study that identifies who are the best supply chains in the world on May 27th at noon Eastern time. Stay up late if you’re in India. Um, we’re going to talk about some of the takeaways from that and what other companies can learn big, small and in the same or in different industries. We can cross pollinate a lot of knowledge across the supply chain professionals to get this, uh, get this information into people’s hands and help them improve themselves and their business.
Scott Luton (01:05:56):
That’s right. Well put and there’s going to be plenty of takeaways and insights regardless of the size of the business that you work release. So join us May 27th you can go to supply chain out radio.com to sign up for trivia. You don’t have to sign up, but it’s helpful if you do, we send out instructions ahead of time. You do need to sign up for the webinar. You can register there, [inaudible] dot com if for some reason you can’t find what you’re looking for, whether it’s something we mentioned on today’s show or something related to one of these two events, or if you want to find a way to collaborate with our supply chain now team, uh, shoot a note over to Amanda at supply chain now, radio.com and we’ll make sure that you get taken care of. Alright, so, uh, Greg, as we wrap here today, great show food supply chain, food safety. Why don’t you take us out?
Greg White (01:06:43):
All right, well first of all, thanks to everyone for joining us. Thanks to Mike and Aubree for sharing a tremendous amount of knowledge and remember, as Scott loves to say, brighter days, lie ahead, join us wherever you get your podcasts, get some, get some uplifting knowledge along with supply chain knowledge and wherever you are, we hope you’re safe and sane and sanguine. I’m going to let you look that one up.
Scott Luton (01:07:12):
Thanks everybody.
Would you rather watch the show in action? Watch as Scott and Greg welcome Mike Wasson and Aubree Duncan to Supply Chain Now through our YouTube channel.
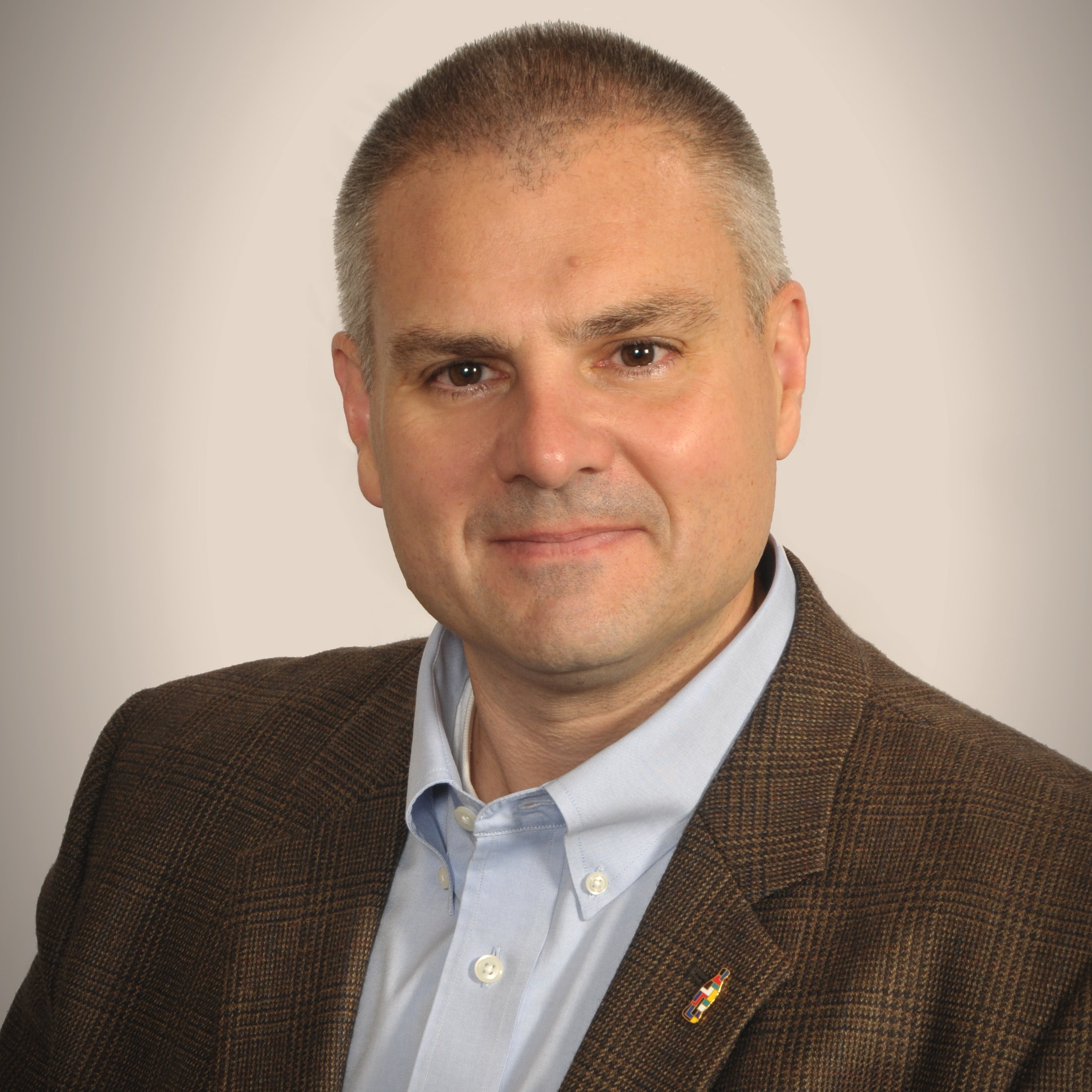
Mike Wasson, CSCP, is chief operations officer at Tosca, an industry leader and innovator, providing a comprehensive portfolio of reusable packaging and supply chain solutions across a diverse range of perishable food markets. In this role, he provides leadership and direction for a state-of-the-art supply chain network, providing unmatched service and lower costs to growers, suppliers and retailers. Wasson has more than 25 years of experience with other industry leaders, including Coca-Cola, DHL Express-USA, YRC Worldwide and Hammacher Schlemmer. He also serves as chairman on the board of directors for the Reusable Packaging Association (RPA), a non-profit trade organization representing and promoting the common and pro-competitive business interests of member suppliers and users of reusable packaging products and services, and fulfilling the promise of a zero-waste, resource-efficient and highly-visible supply chain through reusable packaging. Wasson has previously served the RPA as treasurer-secretary and as chair of the operations and logistics committee. Wasson is also the Chair – Elect for the Association of Supply Chain Management (ASCM), the global leader in supply chain organizational transformation, innovation and leadership. Wasson has previously served on the ASCM and APICS Supply Chain Council board of directors in various leadership and officer positions, and the APICS Corporate Advisory Board.
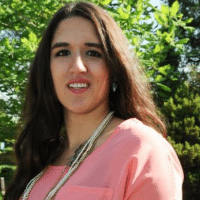
Aubree Duncan is an experienced Food Safety Professional with a demonstrated history of working in commercialization and packaging. Aubree graduated with a Bachelor of Science (B.S.) in Food Science and Technology from Virginia Polytechnic Institute and State University. She has as worked at Tosca for 3 years with progressive roles in leadership of the Food Safety Programs, helping to implement and maintain the system and drive strategic initiatives.
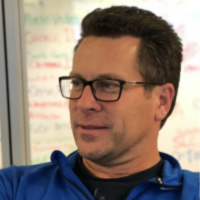
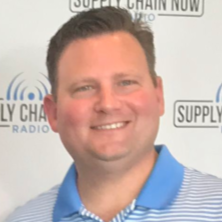
Upcoming Events & Resources Mentioned in this Episode:
Subscribe to Supply Chain Now: supplychainnowradio.com/subscribe/
Connect with Scott on LinkedIn: www.linkedin.com/in/scottwindonluton/
Connect with Greg on LinkedIn: www.linkedin.com/in/gswhite/
Connect with Mike on LinkedIn: www.linkedin.com/in/michael-wasson-69540a9/
Connect with Aubree on LinkedIn: www.linkedin.com/in/aubree-duncan-b7218978/
SCN Ranked #1 Supply Chain Podcast via FeedSpot: tinyurl.com/rud8y9m
SCNR to Broadcast Live at AME Atlanta 2020 Lean Summit: www.ame.org/ame-atlanta-2020-lean-summit
SCNR on YouTube: tinyurl.com/scnr-youtube
2020 AIAG Supply Chain Summit: tinyurl.com/yx5asq35
Key Takeaways from Gartner Supply Chain Top 25 Rankings for 2020 Webinar: tinyurl.com/ybodvlxp
Check Out News From Our Sponsors:
U.S. Bank: www.usbpayment.com/transportation-solutions
Capgemini: www.capgemini.com/us-en/
Vector Global Logistics: vectorgl.com/
APICS Atlanta: apicsatlanta.org
Verusen: www.verusen.com/
ProPurchaser.com: tinyurl.com/y6l2kh7g
Supply Chain Real Estate: supplychainrealestate.com/